Engineered for success: What went into the design of SES’s first HTS satellite
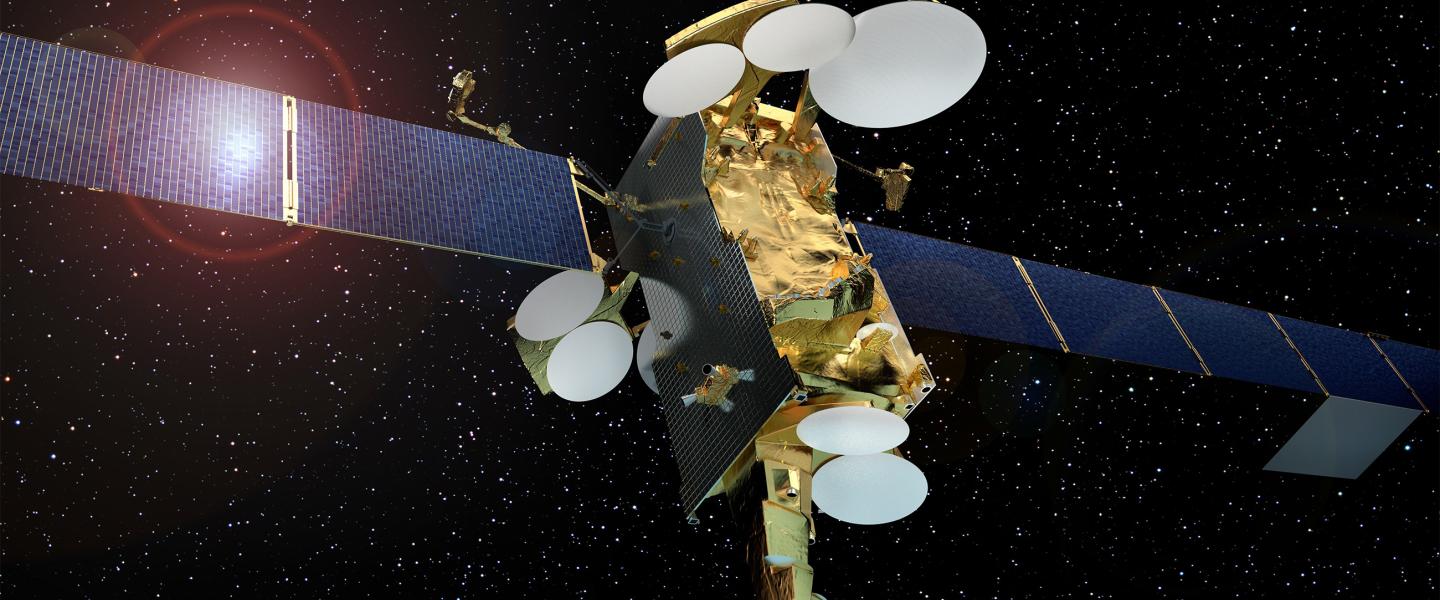
Each satellite put into space generates a certain amount of excitement in the industry, and this is even greater for the upcoming SES-12, SES’s first High Throughput Satellite (HTS).
Vice President of System Architecture Jean-Pierre Choffray, a 14-year SES veteran, gives the lowdown on what went into the design and planning phases of SES-12.
SES-12 will be a replacement for NSS-6, but more importantly it is SES’s first High Throughput Satellite (HTS). Can you tell us more about the technical innovations and how they came about?
It was a process essentially driven by the questions: what capabilities can the new satellite have? How can it satisfy emerging and future business demands? How can we best optimise its design? We had been monitoring the market demands and technology landscape for several years, so our decisions zeroed in on the high-value opportunities across these domains.
For instance, from 95°E- where NSS-6 and SES-8 are co-located - we are currently serving the direct-to-home (DTH) broadcasting needs of around 20 million households in India and Indochina. That sounds like a lot, but we wanted to reach out to the vast areas that remain unserved or underserved, hence the wide-beam transponders. At the same time, with connectivity demands from VSAT, enterprise, mobility, and government applications forming a fast-growing market, we planned for Ku- and Ka-band spot beams capable of delivering over 14 GHz HTS capacity.
With SES-12 having a double mission comprising both traditional wide-beam coverage and high-powered Ku-band multi-spot beam payload, we are looking at a hybrid satellite that gives us immense flexibility. This is enhanced even further with its digital processing ability, which allows us to optimise the allocation of capacity to key growth areas.
Another reason why I am excited about SES-12 is the electric propulsion system that will be used for orbit raising. With this, we have a dramatic reduction in mass which we took advantage of to embark a large and complex payload that we should have severely downscaled in a classical approach.
Can you tell us what it has been like to work on the SES-12?
For over 18 months, I worked closely with at least 50 people from across multiple teams, including systems engineering, spectrum management, business development, finance and sales. The sales team in Asia-Pacific, being close to the ground, know what the customers are asking for, and had insights on which way the market would go.
The team went all out to consolidate interdisciplinary insights, matching the technical realities and trends with technology and business demands. This makes for a richer and more sophisticated blueprint for design. We needed such a highly integrated collaborative effort to decide on the payload we needed, could, and should have.
What was the greatest challenge you faced on the project?
Some of the more prickly issues we faced included severe spectrum restrictions due to Ku-band congestion at 95°E. On top of that, SES-12 is to replace NSS-6, which will be retired in 2017: this meant heavy constraint issues related to the co-location of SES-12 with SES-8, as well as the continuation of the NSS-6 business. The collaboration with the spectrum management team was fundamental to work out these constraints.
With the global scale of our operations, it was also a real test to coordinate the key stakeholders. During the design phase, we held three workshops on one site, for several days at a stretch, to exchange and understand everybody’s priorities, perspectives and needs. These workshops were key to translating SES’s business needs into SES-12’s engineering features.
What technological innovation are you most excited by?
For a long time, there was a question mark on whether or not a Digital Transparent Processor (DTP) would be on-board SES-12. This cutting-edge technology would enable us to offer extreme flexibility in terms of connectivity and thus to adapt to customers’ evolving requirements.
When we first started on the satellite design, the DTP was only an option that we kept open. When, after mapping out our technical and sales roadmaps, the decision was made to embark the DTP on-board, it was a very intense moment of satisfaction for the team – having such innovative technology on-board was very exciting!
On the whole, it was all very, very interesting, and ultimately rewarding to work on this from A to Z. We always want to push the boundaries in our work, not just to enhance the value of customers, but to know that our innovations stand up to future changes and evolutions in demand. You can expect this to be the same for SES-14 and 15 where we continue to challenge ourselves in building for the future.